Automated Machinery Examples
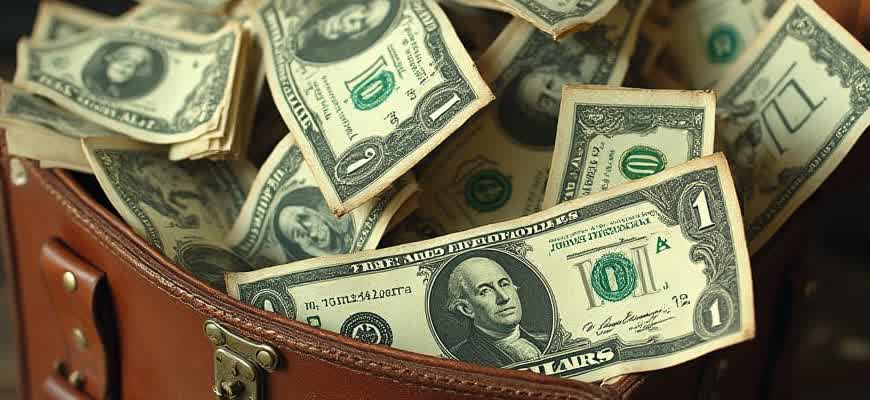
Automated machinery plays a crucial role in modern industries, improving efficiency and reducing human error. Below are some key examples of automated systems in use today.
- Robotic Arms - Commonly used in manufacturing plants, robotic arms perform tasks like welding, assembling, and painting with high precision.
- Automated Guided Vehicles (AGVs) - These mobile robots are used for material transport within warehouses or factories, guided by magnetic or optical systems.
- CNC Machines - Computer Numerical Control machines automate tasks such as drilling, milling, and cutting, ensuring consistent output.
Automated machinery is also integrated into more advanced systems, providing flexibility and adaptability across various industries.
"The use of automated systems has revolutionized production lines, cutting down on labor costs while improving overall productivity."
- 3D Printers - These machines create objects layer by layer based on digital models, used in fields ranging from aerospace to healthcare.
- Automated Packaging Systems - These machines handle packaging, sorting, and labeling products in a fraction of the time it would take manually.
Machine Type | Primary Function | Industry |
---|---|---|
Robotic Arm | Assembly, Welding | Automotive, Electronics |
AGV | Material Transport | Warehousing, Manufacturing |
CNC Machine | Cutting, Drilling | Manufacturing, Metalworking |
Understanding the Role of Robotic Arms in Manufacturing Lines
Robotic arms have revolutionized manufacturing processes, playing an essential role in automating repetitive tasks with high precision. These machines, designed to mimic human arm movements, can perform a variety of functions, from assembly to material handling. With their versatility, robotic arms are crucial for enhancing production efficiency, reducing human error, and improving safety on the factory floor.
In modern production environments, robotic arms are often integrated into assembly lines where they perform operations such as welding, painting, packaging, and testing. These arms are programmed to handle tasks that are too dangerous or monotonous for human workers, thus freeing up personnel for more complex operations. As a result, companies can meet increased demand without compromising quality or safety.
Key Benefits of Robotic Arms in Manufacturing
- Speed and Efficiency: Robotic arms can operate continuously without breaks, increasing throughput and reducing downtime.
- Precision and Consistency: These machines can execute tasks with high precision, ensuring uniformity across all products.
- Workplace Safety: By taking over dangerous tasks, robotic arms help reduce workplace injuries.
Applications of Robotic Arms in Manufacturing
- Assembly: Robotic arms are widely used for assembling parts in industries such as automotive and electronics.
- Welding: These robots provide consistent, high-quality welds for metal components in industries like automotive manufacturing.
- Packaging: Robotic arms handle packaging tasks with precision, ensuring that products are properly wrapped and sealed.
Impact on Manufacturing Efficiency
"Robotic arms not only improve production speed but also enable companies to optimize resources, reduce waste, and maintain high-quality standards."
Comparison of Robotic Arm Types
Robotic Arm Type | Primary Use | Strengths |
---|---|---|
Articulated Arm | Assembly, welding, material handling | Highly flexible, capable of reaching around obstacles |
SCARA | Precision assembly, pick and place tasks | High speed and precision in horizontal motion |
Cylindrical Arm | Packaging, material transfer | Vertical and horizontal motion, suitable for compact spaces |
How Automated Conveyor Systems Enhance Material Handling
Automated conveyor systems are integral to modern production and distribution environments, streamlining the movement of goods within warehouses, factories, and distribution centers. These systems help reduce labor costs and improve the efficiency of material flow by eliminating the need for manual intervention in material transportation. With their ability to handle large volumes of goods at high speeds, conveyors play a crucial role in minimizing delays and improving overall throughput.
By integrating automation into material handling processes, companies can ensure consistent, reliable, and faster movement of products through various stages of production and packaging. This not only increases operational productivity but also enhances safety by reducing the risk of human error and injuries related to manual handling.
Key Benefits of Automated Conveyor Systems
- Increased Efficiency: Automated conveyors ensure continuous, uninterrupted movement of materials, speeding up production cycles.
- Reduced Labor Costs: Automation decreases the dependency on manual labor, reducing overhead costs.
- Improved Safety: With automation, the risk of workplace injuries related to manual handling is significantly lowered.
How Conveyor Systems Improve Material Flow
Automated conveyor systems can be customized to fit specific operational needs, such as directing items through different stages of production, sorting products, or even packaging. Their flexibility makes them highly adaptable to changing production requirements, ensuring that the flow of materials is efficient and aligned with operational goals.
"Conveyor systems are designed to operate seamlessly in various industrial environments, offering scalability and speed that manual processes cannot match."
- Movement: Items are transported swiftly across predefined paths, reducing handling times.
- Sorting: Automated systems can identify and sort products based on size, weight, or barcode readings.
- Tracking: Sensors on conveyor belts track the movement of goods, providing real-time data for inventory management.
Types of Conveyor Systems
Conveyor Type | Advantages |
---|---|
Roller Conveyor | Highly versatile for transporting goods of various shapes and sizes. |
Belt Conveyor | Ideal for moving bulk materials and fragile items over long distances. |
Chain Conveyor | Used for heavy loads and products that need to be moved in harsh environments. |
Exploring the Advantages of Automated Packaging Equipment
Automated packaging machinery plays a crucial role in streamlining production lines by reducing the dependency on manual labor and enhancing operational efficiency. These systems are designed to handle a wide variety of tasks, such as filling, sealing, labeling, and boxing, all while maintaining high levels of precision. Their integration into manufacturing operations brings several advantages, both in terms of productivity and cost-effectiveness.
With the advent of automated packaging, companies can experience a significant reduction in packaging time, increased product consistency, and improved safety on the production floor. Additionally, automation minimizes human error and ensures a faster response to changes in packaging requirements, making it a valuable asset for industries where speed and flexibility are essential.
Key Benefits of Automated Packaging Machinery
- Enhanced Productivity: Automated systems can operate continuously without breaks, significantly increasing throughput and reducing cycle times compared to manual processes.
- Improved Accuracy: Automation minimizes the chances of human error, ensuring each package meets the desired specifications and quality standards.
- Cost Reduction: By decreasing labor costs and reducing material waste, automated systems contribute to substantial cost savings over time.
Automation's Impact on Packaging Efficiency
"Automated machinery provides manufacturers with the ability to handle larger volumes of products at a faster pace, without compromising on quality."
To better understand the value of automated packaging, consider the following table that compares manual and automated packaging processes:
Aspect | Manual Packaging | Automated Packaging |
---|---|---|
Speed | Slow, labor-dependent | Fast, operates 24/7 |
Labor Costs | High due to need for multiple operators | Lower, as fewer workers are needed |
Product Consistency | Subject to human error | Highly consistent with minimal errors |
By incorporating automated packaging solutions, businesses can significantly improve both their operational efficiency and bottom line. The flexibility and reliability of automated systems make them an essential component in modern manufacturing environments.
Integrating AI for Precision Control in CNC Machines
In recent years, the integration of artificial intelligence (AI) into Computer Numerical Control (CNC) machines has significantly enhanced their precision and efficiency. AI algorithms enable real-time monitoring and adjustments during the manufacturing process, improving overall accuracy and reducing errors. This technology also allows CNC machines to optimize their performance by continuously learning from previous tasks, which results in more refined outputs over time.
The introduction of AI in CNC operations has facilitated the implementation of predictive maintenance and adaptive machining techniques. By analyzing machine data and predicting potential failures before they occur, AI reduces downtime and increases the lifespan of CNC equipment. Furthermore, AI-driven systems can adjust machining parameters such as speed, feed rate, and tool paths, ensuring that each part is produced with utmost precision, regardless of complexity.
Key Benefits of AI in CNC Machines
- Enhanced Precision: AI enables real-time adjustments, ensuring consistent accuracy during production.
- Predictive Maintenance: AI systems analyze historical data to anticipate mechanical failures and reduce unplanned downtime.
- Adaptive Machining: AI adapts machine parameters automatically, optimizing processes for different materials and designs.
Real-world Applications
- Tool Path Optimization: AI algorithms adjust the tool path dynamically, improving material removal rates and reducing tool wear.
- Defect Detection: Vision systems integrated with AI can identify defects in the produced parts, ensuring that only flawless components are sent for final assembly.
- Process Control: AI constantly monitors machining conditions and adjusts parameters, such as speed or pressure, to maintain consistent quality across batches.
AI-Driven CNC Machine Performance Comparison
Feature | Traditional CNC | AI-Integrated CNC |
---|---|---|
Precision Control | Manual adjustments by operators | Real-time AI-based adjustments |
Maintenance | Reactive maintenance | Predictive maintenance through AI analysis |
Customization | Limited to pre-set parameters | Dynamic and adaptive customization during operation |
Integrating AI into CNC machines not only improves precision but also enhances their ability to learn and adapt, making them smarter and more efficient with each task they perform.
Key Factors to Consider When Selecting Automated Sorting Systems
When selecting an automated sorting system, businesses must assess various factors to ensure they choose the optimal solution for their operational needs. Sorting systems play a crucial role in improving efficiency, accuracy, and speed in handling goods, but the right system depends on the specific requirements of the warehouse or manufacturing process. Here are some of the main considerations to take into account during the decision-making process.
First, understanding the type of materials or products being handled is essential. The system must be designed to accommodate the size, weight, shape, and fragility of the items. Moreover, operational scalability and flexibility are key, as the system should support potential future expansions or changes in product volume.
1. System Flexibility and Scalability
- Adaptability: The sorting system should be easily adaptable to changes in product types or sizes over time.
- Scalability: Ensure the system can scale to meet future growth in product volumes or operational needs.
- Integration: Consider how well the system integrates with existing machinery, software, and infrastructure.
2. Sorting Speed and Accuracy
- Throughput: The system should be able to handle the required volume of items per hour to meet production deadlines.
- Precision: Accuracy in sorting is vital for minimizing errors and reducing manual corrections.
- Sorting Methods: Evaluate whether the system uses advanced technologies like vision systems or AI-based sorting for improved precision.
It is crucial to evaluate both speed and accuracy when selecting a sorting system. Even the fastest system may fall short if it cannot sort accurately or consistently.
3. Maintenance and Downtime
Ensuring minimal downtime is another critical factor. Consider the maintenance requirements of the system and its potential impact on production. Choose a sorting solution with robust after-sales support, including quick troubleshooting and spare parts availability.
Factor | Consideration |
---|---|
Maintenance | Regular check-ups and easy access to replacement parts |
System Downtime | System should be designed to minimize operational interruptions |
Support | 24/7 technical assistance and service contracts for urgent repairs |
Reducing Labor Costs with Automated Welding Solutions
Automated welding technologies have become essential for industries seeking to optimize production processes and minimize operational expenses. These systems, typically incorporating robotic arms, CNC welding machines, and AI-driven algorithms, are transforming the way welding tasks are approached. By replacing manual labor with automation, companies can significantly reduce the number of workers required and improve the overall efficiency of production lines.
One of the primary benefits of implementing automated welding solutions is the significant reduction in labor costs. Through advanced robotics and machine learning, automated welding systems can perform tasks that were once time-consuming and physically demanding, while maintaining high precision and repeatability. This allows manufacturers to allocate their workforce to more value-added tasks, such as system maintenance, quality control, and design innovation.
Key Benefits of Automated Welding Systems
- Consistent Quality: Robots can perform precise and consistent welds, reducing the variation seen in manual work.
- Reduced Labor Costs: Automation minimizes the need for human operators, resulting in lower wages, benefits, and training costs.
- Increased Productivity: Machines operate at a faster pace and can work around the clock without breaks, leading to higher output.
- Enhanced Safety: Automation reduces the exposure of workers to hazardous environments, such as heat, fumes, and sparks.
Example of Cost Reduction: A Comparative Analysis
Scenario | Labor Costs | Welding Time | Production Volume |
---|---|---|---|
Manual Welding | $50,000/year | 5 hours per unit | 500 units/month |
Automated Welding | $20,000/year | 2 hours per unit | 1000 units/month |
"The integration of automated welding systems can lead to up to 50% reduction in labor costs while doubling production output."
Enhancing Product Consistency with Automated Inspection Tools
In modern manufacturing, achieving uniformity across products is crucial for maintaining quality standards. Automated inspection tools play a significant role in this process, providing manufacturers with the ability to detect deviations in real-time. These tools are integrated into production lines to ensure that each item produced meets specified requirements without the variability introduced by human error.
The use of automated inspection systems leads to more consistent results by leveraging technologies like machine vision and advanced sensors. These systems quickly identify flaws, measure dimensions, and verify other critical aspects of product quality. This level of precision allows manufacturers to make adjustments on the fly, ensuring that production stays within the desired tolerance levels.
Key Benefits of Automated Inspection Systems
- Reduced Human Error: Automation minimizes the chances of mistakes during inspection, ensuring a higher degree of accuracy in quality control.
- Increased Throughput: Automated systems can process products much faster than manual inspections, resulting in higher production efficiency.
- Real-Time Feedback: Automated tools provide immediate feedback, allowing for prompt corrections without halting production.
"Automated inspection tools are vital in ensuring that manufacturing processes remain precise and efficient, leading to a more reliable product output."
Examples of Automated Inspection Tools
- Vision Systems: High-resolution cameras and imaging software detect surface defects, color inconsistencies, and shape deviations.
- Laser Scanning: Laser sensors precisely measure dimensions, helping to ensure that parts conform to exact specifications.
- X-ray Inspection: Used for detecting internal flaws in materials or components that are not visible to the naked eye.
Comparison of Automated Inspection Tools
Tool | Primary Function | Advantages |
---|---|---|
Vision Systems | Surface inspection and defect detection | Fast, versatile, and highly accurate in detecting surface flaws |
Laser Scanning | Dimensional measurement | High precision in measuring part geometry |
X-ray Inspection | Detection of internal flaws | Non-destructive testing for internal integrity |
Challenges and Solutions in Implementing Fully Automated Production
Fully automating production processes brings significant advantages in terms of efficiency, consistency, and cost savings. However, the transition to fully automated systems presents several challenges that must be addressed to ensure a smooth integration. These challenges range from technical difficulties to organizational issues that affect the overall effectiveness of automation in manufacturing environments.
One of the primary obstacles is the high initial investment required for automation systems. This includes costs associated with machinery, software, and training for staff. Overcoming these financial barriers often requires careful planning and a clear understanding of the long-term benefits automation can bring. Additionally, the complexity of retrofitting existing production lines to accommodate automated systems can result in unexpected delays and expenses.
Key Challenges and Their Solutions
- Integration with Existing Systems: Automating production lines that rely on legacy machinery can be a complex task. It is crucial to ensure compatibility between new automated systems and older equipment.
- Skilled Workforce Shortage: Implementing fully automated production requires a highly skilled workforce for setup, maintenance, and monitoring. Training existing employees or hiring new talent is essential to bridge this gap.
- High Upfront Costs: The capital investment needed for automation systems can be daunting for many companies. However, this can be mitigated by implementing phased automation strategies and demonstrating long-term cost savings through increased efficiency and reduced errors.
Effective Solutions
- Incremental Implementation: Gradually introducing automation in phases can help ease the transition and reduce financial strain. This allows companies to assess the system's impact before committing to full-scale automation.
- Employee Training Programs: Investing in training programs for workers ensures that the workforce is equipped with the necessary skills to operate and maintain automated systems effectively.
- Advanced Predictive Maintenance: Leveraging AI and machine learning technologies can help in predicting maintenance needs, reducing downtime, and extending the life of automated equipment.
Successfully navigating the challenges of automation requires a combination of thoughtful planning, the right technological investments, and a focus on employee development. A structured approach can lead to a smoother integration and a more productive future.
Example of Cost Analysis in Automation Implementation
Factor | Initial Cost | Annual Savings |
---|---|---|
Automation Equipment | $1,000,000 | - |
Training and Integration | $100,000 | - |
Labor Cost Reduction | - | $250,000 |
Increased Production Efficiency | - | $300,000 |
Total Savings | - | $550,000 |