8.2 Requirements for Products and Services
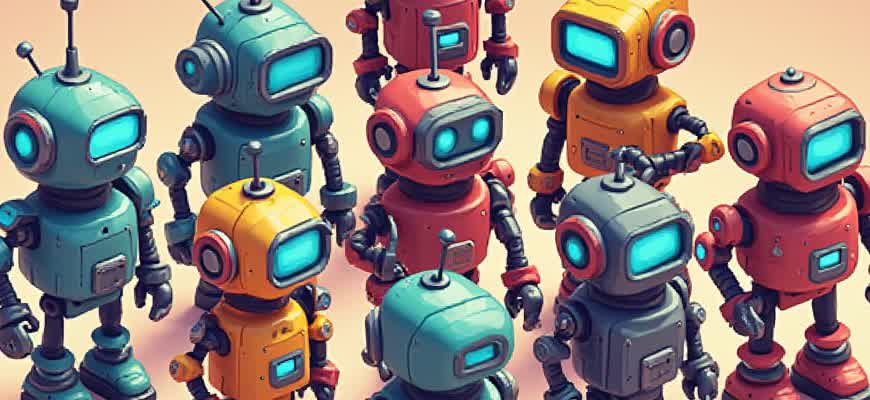
When defining the requirements for products and services, organizations must ensure that they address both customer expectations and regulatory demands. The product development process should be guided by precise specifications, with careful attention to quality, functionality, and performance. Clear documentation and communication channels are critical to align product outcomes with customer needs.
Key Considerations: Requirements must be measurable, achievable, and clearly understood by all stakeholders involved.
To ensure the consistency of product and service offerings, the following steps are essential:
- Identifying customer requirements and expectations through research and feedback.
- Ensuring compliance with relevant industry standards and legal regulations.
- Establishing a clear process for continuous evaluation and improvement.
Specific criteria should be set for product quality, customer satisfaction, and performance efficiency. The organization must also consider the sustainability and lifecycle impact of the product, ensuring it meets long-term operational standards.
Important: Documented processes must be in place to verify that product and service requirements are met at every stage.
These aspects can be summarized in the following table:
Aspect | Description |
---|---|
Customer Needs | Understanding and translating customer requirements into actionable specifications. |
Regulatory Compliance | Adherence to legal and industry standards to ensure product safety and quality. |
Quality Assurance | Processes for testing and validating product performance and durability. |
Environmental Impact | Assessment of product lifecycle to minimize negative ecological effects. |
Defining Product Specifications for Compliance
To ensure products meet legal and regulatory standards, companies must define clear and precise specifications. These specifications form the foundation for assessing whether a product complies with industry regulations, safety standards, and customer expectations. Properly developed product specifications are essential for both manufacturing and quality control processes.
When defining product specifications for compliance, it is crucial to consider the relevant laws, guidelines, and certifications. This includes understanding specific requirements for materials, performance, testing procedures, and labeling. The specifications should also reflect any updates or changes in industry standards to maintain continuous compliance.
Key Steps in Defining Product Specifications
- Identify applicable regulations and standards: Research the relevant compliance frameworks that apply to your product.
- Detail functional and performance requirements: Ensure that your product meets the performance criteria required for its intended use.
- Specify testing methods and conditions: Define the testing protocols that will be used to verify compliance.
- Establish documentation and traceability: Ensure all specifications are clearly documented and traceable for audits and inspections.
- Review and update specifications regularly: Continuously assess the product specifications to ensure they align with any regulatory changes.
Note: Non-compliance with product specifications can result in legal penalties, product recalls, or damage to the company's reputation.
Example Product Specification Table
Specification | Description | Compliance Standard |
---|---|---|
Material Type | High-strength aluminum alloy | ASTM B209 |
Performance | Endure up to 100,000 cycles under load | ISO 9001 |
Temperature Range | -40°C to +85°C | IEC 60721 |
By defining clear product specifications, manufacturers can ensure the product's design, quality, and safety meet regulatory expectations, fostering trust with both customers and regulatory authorities.
Key Quality Standards for Service Delivery
In the context of service delivery, establishing and adhering to quality standards is essential for ensuring customer satisfaction and maintaining operational efficiency. These standards focus on the consistency, reliability, and performance of services provided to clients, ensuring that services meet their needs and expectations. Meeting these criteria also supports continuous improvement and enhances competitive advantage in the marketplace.
There are various frameworks and benchmarks available that help organizations align their services with industry best practices. Adopting these standards ensures that the organization delivers value while mitigating risks associated with service failures and customer dissatisfaction.
Critical Quality Criteria for Service Provision
- Customer Satisfaction - The service should meet or exceed client expectations in terms of quality, timeliness, and communication.
- Consistency - Services should be delivered in a standardized manner, ensuring that clients receive a reliable experience every time.
- Efficiency - Processes should be optimized to minimize waste, reduce costs, and streamline service delivery.
- Compliance - Services must comply with relevant legal, regulatory, and industry-specific requirements.
Key Standards and Frameworks
- ISO 9001 - A globally recognized standard for quality management systems, ensuring that services consistently meet customer requirements.
- Service Level Agreements (SLA) - Defines specific performance benchmarks and expectations, ensuring that services are delivered within agreed-upon timeframes and quality levels.
- Six Sigma - A methodology focused on improving processes by identifying and eliminating defects to enhance service quality.
- ITIL (Information Technology Infrastructure Library) - Provides a set of practices for delivering IT services with a focus on aligning services to business needs.
Ensuring the quality of service delivery requires not only the implementation of standards but also continuous monitoring and improvement to keep up with changing customer needs and expectations.
Service Delivery Performance Metrics
Metric | Purpose |
---|---|
Customer Satisfaction Score (CSAT) | Measures how satisfied customers are with the service received, typically through surveys. |
Net Promoter Score (NPS) | Assesses customer loyalty and their likelihood to recommend the service to others. |
First Response Time | Measures the time taken to respond to a customer’s initial inquiry or request. |
Service Availability | Tracks the uptime of services, ensuring they are consistently available to users as promised. |
Ensuring Compliance with Legal and Regulatory Standards
Ensuring compliance with legal and regulatory standards is a critical aspect of product and service management. Organizations must proactively identify and address all applicable laws and regulations that govern their operations to minimize legal risks and ensure customer satisfaction. This involves both internal policies and external regulatory frameworks that can vary by industry and geography. Failing to comply with legal requirements can lead to severe financial penalties, reputational damage, or even operational shutdowns.
To effectively ensure compliance, businesses must establish clear processes for identifying relevant laws, monitoring changes, and integrating these requirements into their product or service development lifecycle. This process should be supported by continuous training and regular audits to verify that all departments adhere to these standards.
Key Steps for Compliance
- Identify Relevant Laws: Conduct a thorough review of local, national, and international regulations that affect product development and service delivery.
- Integrate Compliance into Design: Ensure that legal requirements are factored into every stage of product development, from design to delivery.
- Monitor Changes: Stay updated on regulatory changes and adapt the product or service offerings as needed to maintain compliance.
- Audit and Verify: Regularly audit internal processes and systems to ensure adherence to legal standards and rectify any discrepancies promptly.
Regulatory Compliance Overview
Regulatory Area | Impact on Product/Service | Compliance Measures |
---|---|---|
Data Privacy | Ensures user data is protected and not misused | Adhere to GDPR, CCPA, or other data protection laws |
Health and Safety | Guarantees that products and services do not pose health risks | Follow OSHA standards, conduct risk assessments |
Environmental Regulations | Limits environmental impact of products | Comply with EPA, RoHS, and other environmental laws |
Important: Consistent monitoring and adaptation to new legal requirements are crucial to maintaining long-term compliance and avoiding potential fines.
Managing Customer Expectations in Product Design
Effectively managing customer expectations during product design is crucial for creating products that meet market demands and build customer loyalty. It involves balancing customer desires with practical limitations such as time, cost, and technical capabilities. Product teams need to communicate clearly with stakeholders and define realistic goals from the outset to avoid misunderstandings or dissatisfaction later in the development process.
Setting accurate expectations is not just about telling customers what a product will do, but also about managing how it is communicated, ensuring that each phase of design is aligned with the customer's evolving needs. Clear documentation, iterative feedback, and proactive risk management are essential tools in this process.
Key Strategies to Manage Expectations
- Early and Transparent Communication: Involve the customer early in the design process and regularly update them on progress. This helps ensure alignment and reduces surprises.
- Set Realistic Timelines: Clearly define product milestones and expected delivery dates to prevent overpromising and underdelivering.
- Prioritize Features: Identify core product features and communicate any trade-offs or limitations in the design phase to avoid dissatisfaction later.
Techniques for Aligning Customer Needs with Product Capabilities
- Define Clear Requirements: Collect detailed requirements from customers, including functional and non-functional specifications, to avoid ambiguities.
- Prototyping and Testing: Use prototypes and pilot tests to gather real-world feedback, which can help refine product features early in the design process.
- Regular Feedback Loops: Continuously involve customers in feedback sessions to ensure the product aligns with their needs at every stage.
Note: Properly managing customer expectations during the product design phase increases the likelihood of customer satisfaction and long-term product success.
Managing Risks in Customer Expectations
Risk | Management Strategy |
---|---|
Unclear Requirements | Conduct detailed discovery sessions and maintain continuous communication with customers. |
Overpromising Features | Prioritize features based on importance and communicate limitations transparently. |
Delayed Timelines | Set realistic deadlines and provide updates if adjustments are needed. |
Streamlining Service Implementation for Consistency
Ensuring consistency in the delivery of services is essential for maintaining high-quality standards and meeting customer expectations. A streamlined implementation process helps reduce errors, improve efficiency, and enhance the overall service experience. By establishing clear guidelines and standardized procedures, organizations can deliver services that consistently meet predetermined criteria, aligning with customer requirements and industry standards.
A well-organized service implementation process involves careful planning, precise execution, and continuous evaluation. The use of standardized tools, templates, and frameworks ensures that all services are delivered in a uniform manner, which is critical for long-term success and customer satisfaction.
Key Elements of Streamlined Service Implementation
- Standard Operating Procedures (SOPs): Documenting each step of the service delivery process allows for uniformity in execution. SOPs should be easily accessible and updated regularly to reflect any process improvements or regulatory changes.
- Role Definition and Accountability: Clear roles and responsibilities ensure that every team member knows their part in the process, leading to fewer mistakes and more efficient operations.
- Technology Integration: Using automated systems and tools to track progress and manage tasks reduces manual intervention, making the service implementation process more reliable and faster.
Best Practices for Achieving Consistency
- Develop a detailed service blueprint that outlines every aspect of service delivery, from initial client contact to post-delivery follow-up.
- Regularly train staff on the latest procedures and technologies to ensure that they are equipped to follow the defined processes correctly.
- Implement continuous monitoring and feedback loops to detect inconsistencies early and make corrective adjustments promptly.
Important: Streamlining service implementation is not a one-time effort but a continuous process that requires regular updates and assessments to ensure ongoing consistency and quality.
Monitoring and Improvement
Area | Focus | Action |
---|---|---|
Process Documentation | Ensure clarity and completeness | Regularly review and update SOPs |
Staff Training | Enhance skill set | Provide ongoing training sessions |
Feedback Mechanisms | Identify potential gaps | Use client feedback for continuous improvement |
Meeting Industry-Specific Requirements for Products
To ensure that products are fit for their intended use in specific sectors, manufacturers must meet industry-specific standards. These standards govern various aspects, from safety and environmental considerations to performance metrics, ensuring that the products fulfill customer expectations and regulatory demands. Each industry establishes its own set of regulations that companies must comply with to avoid legal issues and protect consumer safety.
Adhering to these specific requirements involves understanding the unique demands of each market and designing products that meet these standards. The process includes rigorous testing, validation, and certification to demonstrate that products function as intended and are free of defects that could pose risks. Meeting these standards is vital not only for market entry but also for maintaining a strong brand reputation and customer trust.
Examples of Industry Standards
- Automotive: Products like vehicle components must adhere to safety standards such as crash tests and environmental regulations, including emissions control.
- Medical Devices: Compliance with regulations like ISO 13485 ensures that medical equipment is safe, reliable, and effective for patient use.
- Food Industry: Food products need to comply with health and safety standards such as HACCP to prevent contamination and ensure quality.
Key Factors to Consider
- Material Safety: Ensuring that materials used are safe for their intended use, such as non-toxic and durable, is crucial in many industries.
- Environmental Impact: Many industries require products to meet eco-friendly standards, like minimal environmental footprint during production.
- Performance Testing: Industry standards often mandate comprehensive performance testing to verify that products meet efficiency and reliability benchmarks.
Important: Failure to meet industry-specific standards can result in recalls, fines, or legal action, severely damaging a company's reputation and operations.
Industry | Standard | Description |
---|---|---|
Construction | ISO 9001 | Defines quality management standards to ensure that construction materials and processes meet international quality assurance guidelines. |
Pharmaceuticals | GMP | Good Manufacturing Practices ensure that drugs and medicines are produced to meet quality and safety standards. |
Electronics | CE Marking | Indicates that a product complies with European Union regulations for safety, health, and environmental protection. |
Integrating Feedback Loops for Continuous Improvement
To ensure the consistent enhancement of products and services, the incorporation of feedback loops is essential. These loops allow for the ongoing collection, analysis, and application of feedback from customers, stakeholders, and internal teams. The systematic integration of feedback mechanisms plays a critical role in identifying areas of improvement, driving innovation, and ensuring that products and services meet or exceed expectations.
By fostering a culture of continuous feedback, organizations can quickly adapt to changing market demands, address potential issues before they escalate, and improve customer satisfaction. This approach not only enhances operational efficiency but also strengthens the long-term viability of the product or service in the marketplace.
Key Feedback Mechanisms
- Customer Surveys: Regular surveys provide insights into customer satisfaction and product performance.
- Social Media Monitoring: Tracking online discussions helps identify emerging trends and issues.
- Internal Reviews: Feedback from employees who directly interact with the product can pinpoint internal inefficiencies.
- Usage Data Analytics: Collecting data on how users interact with the product reveals patterns for improvement.
Steps for Implementing Feedback Loops
- Establish Feedback Channels: Create multiple avenues for feedback, such as surveys, customer service interactions, and digital platforms.
- Analyze Feedback: Systematically analyze collected data to uncover trends, issues, and opportunities.
- Implement Changes: Based on feedback, prioritize and implement necessary improvements in products or services.
- Monitor Impact: Track the results of implemented changes to ensure they address the identified needs.
Example of a Feedback Loop
Step | Action |
---|---|
1 | Collect customer feedback via surveys |
2 | Analyze feedback to identify improvement areas |
3 | Implement changes to the product based on feedback |
4 | Monitor customer response after changes are made |
"Incorporating feedback loops into your product development process ensures that continuous improvement becomes an integral part of your organizational culture."
Documentation and Reporting of Product and Service Conformance
Ensuring that products and services meet specified requirements is a critical aspect of maintaining quality standards. This process requires precise documentation to verify that all attributes and features conform to the expected criteria. Documenting product and service conformance helps to maintain transparency, enhance trust, and provide a clear audit trail for regulatory and customer requirements. Reports are typically generated at various stages, including pre-production, during production, and after delivery, ensuring continuous monitoring and compliance.
Comprehensive reporting is vital for tracking the progress of conformity assessments and for identifying areas requiring improvement. Reports should outline conformity test results, corrective actions taken, and any deviations from the original specifications. Clear, structured documentation also serves as a tool for both internal and external stakeholders to evaluate whether the delivered product or service meets contractual and legal obligations.
Key Elements of Conformance Documentation
- Test Results: Detailed records of tests performed to assess product characteristics.
- Compliance Certificates: Formal documentation confirming adherence to specific standards or regulations.
- Inspection Reports: Documentation of visual and functional inspections conducted at various stages of production.
- Corrective Action Logs: Records detailing any issues found and the actions taken to address them.
Reporting Process
- Preparation of Reports: Gather all relevant data from tests, inspections, and audits.
- Analysis of Results: Review results to identify any discrepancies or non-conformities.
- Action Plan: Develop an action plan if discrepancies are found, outlining corrective measures.
- Final Report: Compile a comprehensive report summarizing all findings and actions taken.
Note: Conformance documentation should be regularly reviewed and updated to reflect changes in product design, regulations, or customer requirements.
Table of Conformance Report Elements
Report Element | Description | Frequency of Update |
---|---|---|
Test Results | Documentation of test outcomes related to product specifications. | As tests are completed |
Compliance Certificates | Formal certificates indicating compliance with relevant standards. | Annually or as standards are updated |
Inspection Reports | Details of physical inspections and product assessments. | During each inspection phase |
Corrective Actions | Logs of any corrective actions taken to address non-conformities. | As corrective actions are implemented |