Adopting Internet of Things for Manufacturing Firms Business Model Development
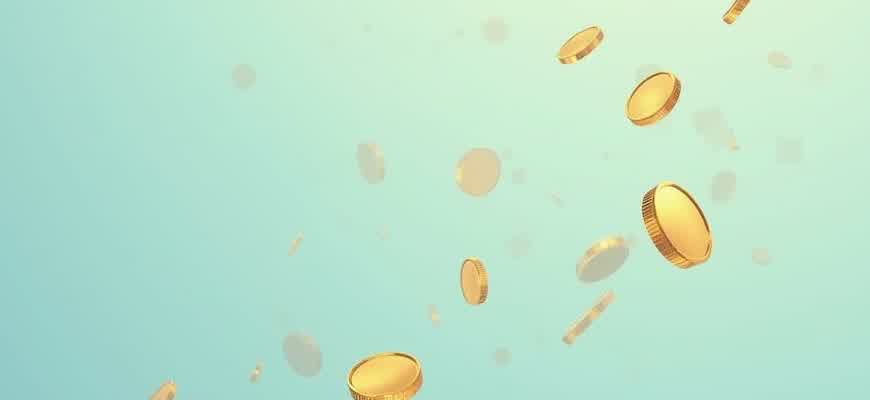
The rapid evolution of Internet of Things (IoT) technologies has significantly impacted manufacturing operations. By incorporating IoT systems, businesses can enhance operational efficiency, improve data analysis capabilities, and optimize production processes. Manufacturers can connect their equipment, sensors, and devices in real-time to monitor performance, predict maintenance needs, and streamline supply chains. These advancements not only enable better decision-making but also drive cost reductions and boost productivity.
To successfully incorporate IoT into a manufacturing business model, firms must address key elements such as infrastructure, data management, and workforce adaptation. Below are the essential components for integrating IoT technologies:
- Infrastructure: Invest in reliable sensors and communication networks to enable seamless connectivity across production lines.
- Data Management: Implement robust data storage and processing systems to handle the massive volume of information generated by IoT devices.
- Workforce Adaptation: Train employees to understand and leverage new IoT tools, ensuring smooth implementation and integration with existing systems.
"The adoption of IoT technologies in manufacturing not only improves efficiency but also opens the door to new business opportunities and revenue streams."
As the manufacturing landscape continues to evolve, IoT plays a crucial role in shaping the future of business models. Manufacturers who effectively harness these technologies can unlock a wide range of benefits, from predictive maintenance to real-time supply chain visibility, enhancing both operational and financial performance.
Integrating IoT Devices into Existing Manufacturing Systems
Integrating Internet of Things (IoT) devices into traditional manufacturing systems is a critical step for improving efficiency and gaining real-time insights. IoT devices, ranging from sensors to smart machinery, enable manufacturers to collect data that was previously unavailable or difficult to analyze. This seamless integration allows businesses to monitor processes, predict maintenance needs, and optimize production lines more effectively. However, this process requires careful planning to ensure compatibility with existing infrastructure and to minimize disruption during implementation.
Successful integration involves multiple stages, including selecting appropriate devices, connecting them to existing software, and ensuring that data flows correctly between systems. It is essential for manufacturers to evaluate their current operations and identify specific areas where IoT can add value. This can involve anything from improving inventory management to enhancing equipment uptime, thus streamlining operations and reducing costs.
Key Considerations for IoT Integration
- Device Compatibility: Ensure that new IoT devices are compatible with legacy systems, or plan for necessary upgrades.
- Data Security: Protect data by integrating strong encryption and access controls, as IoT devices can be vulnerable to cyber threats.
- Scalability: Consider the future needs of the business and select devices that can scale with the growth of the operations.
- Employee Training: Ensure that employees are adequately trained to work with new systems and devices.
Implementation Steps
- Assessment: Conduct an assessment of current systems to identify integration opportunities.
- Device Selection: Choose IoT devices that meet the specific needs of the manufacturing process.
- System Integration: Integrate IoT devices with existing manufacturing management software.
- Testing: Run tests to ensure seamless communication between devices and systems.
- Training: Train staff to handle new technology and troubleshoot issues.
Impact of IoT on Manufacturing Efficiency
Factor | Before IoT Integration | After IoT Integration |
---|---|---|
Data Availability | Limited data, often manually recorded | Real-time data from sensors and devices |
Maintenance | Reactive maintenance based on breakdowns | Predictive maintenance using data insights |
Efficiency | Manual processes with occasional downtime | Automated, optimized processes with minimal downtime |
By leveraging IoT technologies, manufacturers can not only enhance their operational efficiency but also ensure better decision-making through data-driven insights. This proactive approach can significantly reduce waste and increase production reliability.
Data-Driven Decision Making in Manufacturing through IoT
The integration of IoT technologies into manufacturing operations has revolutionized the way businesses collect and analyze data. By deploying sensors and connected devices throughout production lines, companies can now track real-time performance metrics, environmental conditions, and equipment status. This continuous flow of data enables manufacturers to move beyond traditional decision-making processes, offering a more precise and dynamic approach to management. With IoT, decisions are made based on current data, improving operational efficiency and reducing human error.
Leveraging data from IoT systems allows manufacturers to optimize every aspect of their processes, from supply chain management to product quality control. The ability to process vast amounts of data in real time enables manufacturers to react promptly to issues, forecast maintenance needs, and streamline production workflows. In turn, this leads to a more responsive business model, with the potential to adapt quickly to market changes and customer demands.
Key Benefits of Data-Driven Decision Making in Manufacturing
- Increased operational efficiency: Continuous data collection allows for better resource allocation and reduces downtime.
- Predictive maintenance: IoT devices can monitor equipment health, predicting failures before they occur and minimizing unexpected breakdowns.
- Real-time monitoring: Immediate access to data from production lines enables swift decisions on adjustments to improve output quality.
- Enhanced product quality: Data analysis helps identify areas for improvement in production, resulting in consistent product quality.
Implementation Process for IoT-Driven Data Collection
- Deploy IoT devices: Install sensors and connected systems across critical points in the production line.
- Data integration: Ensure seamless integration of IoT-generated data with existing IT infrastructure and data management systems.
- Data analysis: Use advanced analytics platforms to process the collected data and generate actionable insights.
- Decision making: Make informed decisions based on real-time data, enhancing process optimization and product development.
By utilizing IoT, manufacturers gain unprecedented visibility into their operations, which allows for smarter, data-driven decisions that improve both short-term results and long-term growth.
Example of IoT-Driven Data Analysis in Manufacturing
Aspect | Traditional Process | IoT-Enhanced Process |
---|---|---|
Production Monitoring | Manual checks and reports | Real-time sensor data analysis |
Maintenance | Scheduled or reactive | Predictive maintenance based on sensor data |
Quality Control | Spot checks and manual inspections | Continuous quality tracking with IoT-enabled sensors |
Optimizing Supply Chain Management with IoT Solutions
With the increasing complexity of supply chains, manufacturing firms are leveraging Internet of Things (IoT) technologies to enhance efficiency and reduce costs. IoT solutions allow real-time monitoring of products, assets, and environmental conditions, leading to better decision-making and seamless operations. Through interconnected devices, manufacturers can track every stage of the supply chain, from raw material procurement to final product delivery.
Implementing IoT in supply chain management offers several benefits. The integration of smart sensors and data analytics enables firms to predict demand fluctuations, optimize inventory levels, and reduce lead times. These innovations enhance visibility across the supply chain, resulting in proactive problem-solving and higher operational agility.
Key Benefits of IoT in Supply Chain Optimization
- Real-time Tracking: IoT enables constant monitoring of shipments and inventory, ensuring that businesses stay informed on the status of materials and products throughout the supply chain.
- Improved Demand Forecasting: By analyzing historical data and market trends, IoT systems can predict future demands, enabling companies to adjust production plans accordingly.
- Enhanced Predictive Maintenance: IoT sensors can detect potential failures in equipment before they happen, reducing downtime and improving overall equipment efficiency.
- Optimized Routing and Logistics: IoT allows for dynamic route adjustments based on real-time traffic, weather, and location data, reducing transportation costs and improving delivery times.
Practical Implementation of IoT in Supply Chains
- Sensor Deployment: Attach smart sensors to products, packaging, and vehicles for real-time data collection, such as temperature, location, and condition of goods.
- Data Analytics Integration: Use advanced analytics to interpret the data gathered from IoT devices and provide actionable insights to optimize inventory and logistics operations.
- Automation of Operations: Implement automated systems for inventory management, order fulfillment, and route planning based on IoT data, reducing human error and increasing operational efficiency.
"IoT-driven solutions are transforming the way manufacturing companies manage their supply chains, shifting from reactive to proactive decision-making."
Impact on Operational Performance
The integration of IoT not only improves real-time decision-making but also enhances overall operational performance. For example, inventory management becomes more accurate, and shipping routes are optimized, reducing both costs and delays. IoT systems provide the capability to track and adjust logistics operations dynamically, ensuring that manufacturing firms maintain smooth and cost-effective supply chain processes.
Comparison of Traditional vs IoT-Optimized Supply Chain
Aspect | Traditional Supply Chain | IoT-Optimized Supply Chain |
---|---|---|
Visibility | Limited, based on manual updates | Real-time, with continuous tracking |
Inventory Management | Periodic checks, manual forecasting | Automated, data-driven forecasting |
Operational Efficiency | Often reactive, prone to delays | Proactive, reducing delays and costs |
How IoT Enables Predictive Maintenance in Manufacturing
Predictive maintenance (PdM) is one of the most significant advancements enabled by the Internet of Things (IoT) in manufacturing. With the integration of IoT devices, manufacturers can now continuously monitor the condition of machinery and equipment in real-time. By collecting data on parameters such as temperature, vibration, pressure, and humidity, IoT sensors provide a comprehensive view of asset performance, making it easier to predict potential failures before they occur.
Through data analysis and machine learning algorithms, these insights allow manufacturers to move from reactive maintenance to proactive strategies. This shift leads to optimized maintenance schedules, reduced downtime, and extended equipment lifecycles, all of which directly contribute to cost savings and operational efficiency.
How IoT Works for Predictive Maintenance
- Data Collection: IoT sensors are attached to critical machinery to gather real-time data on performance indicators.
- Data Transmission: The gathered data is transmitted to a centralized system, often in the cloud, for further processing.
- Data Analysis: Advanced algorithms analyze this data to identify patterns and detect early signs of potential issues.
- Maintenance Alerts: Based on analysis, alerts are sent to the maintenance team with specific recommendations for action.
Key Benefits of IoT in Predictive Maintenance
- Reduced Downtime: By predicting failures, maintenance can be scheduled during non-critical periods, avoiding unplanned downtime.
- Cost Efficiency: Predictive maintenance helps minimize repair costs and extends the life of expensive machinery.
- Improved Safety: Continuous monitoring ensures that machines are operating within safe parameters, reducing the risk of hazardous failures.
- Optimized Resource Allocation: Maintenance efforts are focused only on equipment that needs attention, improving the efficiency of the workforce.
IoT Data Analysis for Predictive Maintenance
Data Type | Analysis Type | Benefit |
---|---|---|
Vibration | Detects misalignment, imbalance, or wear in rotating machinery | Helps prevent equipment failure due to mechanical issues |
Temperature | Monitors abnormal temperature fluctuations | Prevents overheating or overcooling, ensuring efficient operation |
Pressure | Identifies abnormal pressure patterns in hydraulic systems | Indicates potential leaks or blockages, ensuring system integrity |
Humidity | Detects moisture buildup | Prevents corrosion and electrical failures |
"The IoT-driven approach to predictive maintenance shifts the focus from reactive to proactive, allowing manufacturers to detect issues early and plan maintenance activities more effectively."
Reducing Operational Costs with IoT Automation
Integrating IoT-based automation into manufacturing processes offers significant advantages in cutting operational costs. By utilizing connected devices and sensors, companies can track real-time data on machine performance, inventory levels, and energy consumption. This level of visibility enables manufacturers to streamline operations, reduce downtime, and optimize resource usage, ultimately resulting in cost savings across various departments.
Moreover, IoT systems facilitate predictive maintenance, a strategy that reduces the need for reactive repairs. With sensors monitoring equipment health, the system can predict failures before they occur, leading to fewer unplanned outages and extending the lifespan of machinery. This transition from manual to automated operations enhances overall operational efficiency.
Key Benefits of IoT Automation in Cost Reduction
- Energy Efficiency: IoT-enabled smart meters and sensors monitor energy usage, automatically adjusting systems to minimize waste.
- Predictive Maintenance: Sensors detect potential issues in advance, reducing costly emergency repairs and unplanned downtime.
- Reduced Labor Costs: Automation reduces the need for manual intervention, freeing up human resources for higher-value tasks.
Operational Cost Reduction Examples
Aspect | Before IoT Automation | After IoT Automation |
---|---|---|
Machine Downtime | Frequent unplanned stops | Reduced downtime with predictive alerts |
Energy Usage | High energy waste | Optimized energy consumption |
Maintenance Costs | Costly emergency repairs | Lower maintenance costs due to early issue detection |
"By leveraging IoT automation, manufacturers can not only cut direct costs but also enhance productivity and create a more sustainable operation model."
Improving Quality Assurance in Manufacturing with IoT Integration
In the context of manufacturing, quality control is crucial for maintaining product consistency and meeting industry standards. The traditional methods of quality inspection often face challenges in terms of speed, accuracy, and real-time monitoring. With the introduction of IoT technologies, manufacturers can enhance the precision and efficiency of quality control processes. By integrating smart sensors and devices throughout the production line, businesses can continuously monitor various product parameters and detect potential defects early.
The application of IoT in quality assurance allows manufacturers to gather real-time data on critical aspects such as temperature, pressure, humidity, and material composition. This data can then be analyzed using advanced analytics to identify trends, forecast issues, and prevent defects before they occur. The result is a more reliable and cost-efficient approach to maintaining high product standards, with minimal human intervention.
Key Benefits of IoT in Product Quality Control
- Real-Time Monitoring: Continuous tracking of production parameters ensures that quality issues are identified and addressed immediately.
- Predictive Analytics: By analyzing historical data, manufacturers can predict potential quality deviations and adjust processes proactively.
- Automated Quality Checks: IoT-enabled systems can automatically verify product specifications and ensure compliance with standards, reducing the need for manual inspection.
Examples of IoT-Driven Quality Control in Manufacturing
- Smart Sensors in Production Lines: Sensors embedded in machinery can detect anomalies such as equipment malfunctions or product defects, alerting operators to take immediate action.
- Data-Driven Decision Making: Collected data can be analyzed to optimize production processes, ensuring better quality outcomes and minimizing waste.
- Automated Defect Detection: IoT systems can be integrated with vision systems to automatically detect imperfections in the product surface, such as cracks or dents.
By adopting IoT technologies in quality control, manufacturers can significantly reduce the risk of defects, enhance production efficiency, and ensure that each product meets the highest standards.
IoT-Enabled Data Monitoring: Key Metrics for Quality Assurance
Metric | Description | Impact on Quality |
---|---|---|
Temperature | Monitor temperature during manufacturing processes that are sensitive to heat. | Ensures consistency in the material properties, preventing defects. |
Pressure | Detect pressure variations in machines or material handling systems. | Prevents issues like over-pressurization, which could lead to faulty products. |
Vibration | Track vibration levels in machinery. | Helps detect mechanical wear and tear early, preventing machinery failure and maintaining product quality. |
Securing IoT Networks and Data in Manufacturing Environments
In the context of manufacturing environments, securing IoT networks and the data they generate is critical to ensure operational continuity, protect intellectual property, and comply with regulatory requirements. As more connected devices are integrated into industrial processes, the potential for cyberattacks and data breaches increases, making robust cybersecurity measures essential. Manufacturing firms must adopt a comprehensive security strategy that covers both physical devices and the digital networks they communicate through.
Effective security practices for IoT in manufacturing go beyond traditional network defense methods, requiring specialized protocols to safeguard connected systems from vulnerabilities. A multi-layered approach that includes device authentication, data encryption, and continuous monitoring is fundamental for maintaining system integrity and preventing unauthorized access. Below are key strategies for securing IoT networks and data.
Key Security Measures for IoT in Manufacturing
- Device Authentication: Ensuring that only authorized devices are allowed to connect to the network through secure authentication methods like digital certificates or biometric verification.
- Data Encryption: Encrypting data both in transit and at rest to protect sensitive information from being intercepted or tampered with during communication between devices.
- Network Segmentation: Dividing the network into isolated segments to limit the impact of potential breaches, ensuring that compromised devices cannot easily access critical manufacturing systems.
- Regular Software Updates: Keeping all connected devices and systems up-to-date with the latest security patches to address newly discovered vulnerabilities.
- Intrusion Detection Systems: Deploying real-time monitoring systems to detect unusual activity and potential threats, enabling quick responses to mitigate damage.
Best Practices for Securing Manufacturing IoT Systems
- Implement Strong Access Control: Limit access to critical systems to only those who require it, using role-based access controls and multi-factor authentication.
- Conduct Regular Security Audits: Perform periodic reviews and penetration testing to identify vulnerabilities and ensure security measures are effective.
- Develop Incident Response Plans: Prepare for potential breaches by establishing procedures for identifying, responding to, and recovering from security incidents.
Security Challenges in IoT Integration
Challenge | Impact | Solution |
---|---|---|
Device Heterogeneity | Diverse devices may have varying security standards, complicating network integration. | Standardize security protocols across devices to ensure uniform protection. |
Data Privacy Concerns | Sensitive data may be exposed during transmission or storage, risking breaches. | Implement end-to-end encryption and ensure strict access controls. |
Continuous Monitoring | Monitoring IoT systems 24/7 can be resource-intensive and challenging to manage. | Deploy automated monitoring tools to detect and respond to threats in real time. |
"A proactive security strategy in IoT manufacturing environments is essential for mitigating risks and ensuring the integrity of both the physical and digital assets."