How Much Is the Homemade Method
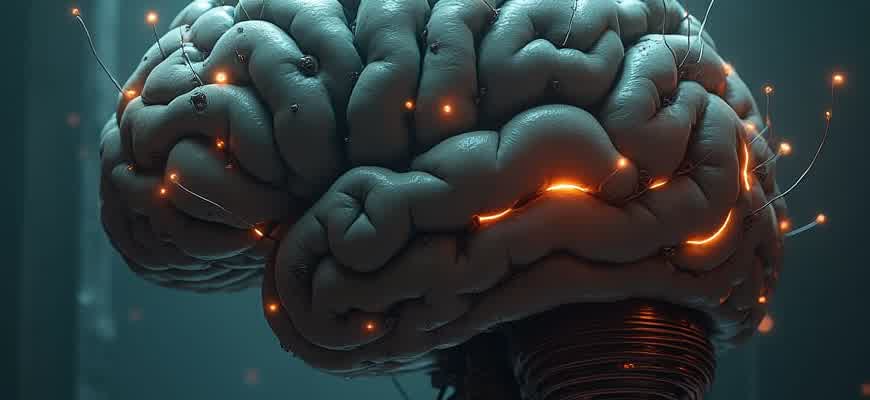
Creating products or solutions at home can significantly reduce expenses, but it's essential to break down each component to understand the actual savings. Here's what you typically pay for in a do-it-yourself setup:
- Materials: Raw inputs required for the project
- Tools: Equipment necessary for production or assembly
- Time: The hours invested in building, testing, and adjusting
- Knowledge: Learning resources or consultations
DIY solutions may appear economical, but hidden costs–like tool wear and trial-and-error mistakes–can add up quickly.
To compare typical expenditures for a homemade setup versus a commercial purchase, consider this simplified table:
Expense Category | DIY Estimate | Retail Alternative |
---|---|---|
Materials | $30 | Included in price |
Tools | $50 (one-time) | Not required |
Labor Time | 6 hours | 0 hours |
Total Initial Cost | $80 + time | $100 |
While the upfront investment may be lower with DIY, the value of time and efficiency should not be overlooked.
Evaluating Material Expenses in DIY Projects
When planning a hands-on creation, precise budgeting begins with understanding what each component costs. Breaking down material expenses allows you to assess whether a project is truly more affordable than a store-bought equivalent. Focus on individual units, weight, or volume depending on how the ingredients are sold.
To get an accurate total, determine the quantity of each item needed and calculate the price per unit. Avoid rounding–small discrepancies across multiple materials can lead to significant miscalculations.
Steps to Calculate Costs Accurately
- List every required ingredient or component.
- Note the amount needed for the project.
- Find the cost of the product in its packaging size.
- Convert the cost to the needed amount using basic division and multiplication.
Always base calculations on the unit price. If flour costs $2.50 for 2 kg and you only need 500 g, use: (2.50 ÷ 4) = $0.625
Item | Needed | Package | Package Cost | Cost Used |
---|---|---|---|---|
Beeswax | 200 g | 500 g | $8.00 | $3.20 |
Olive Oil | 100 ml | 1 L | $6.00 | $0.60 |
- Use bulk prices for better cost-efficiency analysis.
- Record all prices and amounts for future reuse.
- Recalculate if changing brands or suppliers.
How to Calculate the Value of Your Personal Labor
When tackling a project on your own, it's crucial to assign a tangible value to the time you invest. Ignoring the worth of your hours can create a false sense of savings and distort cost comparisons with professional services.
To assess the true expense of your time, consider your current or potential hourly wage. Then, track the hours required to complete each stage of the task. This approach reveals whether the DIY route is genuinely economical or just labor-intensive.
Steps to Quantify Your Time Investment
- Identify your equivalent hourly rate (use your job income or freelance rate).
- Break the project into segments: planning, sourcing, execution, correction.
- Record time spent on each segment honestly.
- Multiply total hours by your hourly rate.
Note: If your calculated time cost exceeds the price of outsourcing, DIY may not be the best option unless other factors (like skill-building or satisfaction) apply.
- Planning: Research, designing, and listing materials.
- Acquisition: Shopping for tools and supplies.
- Execution: Building, assembling, or crafting.
- Correction: Fixing mistakes or refinishing work.
Phase | Hours Spent | Cost (@$25/hr) |
---|---|---|
Planning | 3 | $75 |
Acquisition | 2 | $50 |
Execution | 6 | $150 |
Correction | 1 | $25 |
Total | 12 | $300 |
Comparing Homemade vs. Store-Bought: A Cost Breakdown
Preparing items from scratch at home often seems cheaper at first glance, but the actual cost comparison depends on multiple variables, such as ingredient pricing, equipment needs, and batch size. In this breakdown, we’ll analyze common factors that impact overall cost when making things yourself versus purchasing them ready-made.
To illustrate, we'll examine a specific example: baking a loaf of sourdough bread. The table below outlines ingredient costs, energy usage, and store-bought pricing to show the true cost-per-unit in each case.
Cost Analysis: Homemade Sourdough Bread vs. Bakery Loaf
Component | Homemade (per loaf) | Store-Bought |
---|---|---|
Flour, Water, Salt, Starter | $0.90 | – |
Electricity (baking 1 hr) | $0.25 | – |
Initial Equipment (amortized) | $0.20 | – |
Total Cost | $1.35 | $4.50 |
Even with equipment and utility costs factored in, homemade sourdough bread is approximately 70% cheaper per loaf.
- Homemade Pros: Lower cost per unit, control over ingredients, long-term savings.
- Homemade Cons: Time-consuming, requires skill and initial investment in tools.
- Store-Bought Pros: Convenience, consistent quality, no prep time.
- Store-Bought Cons: Higher price, less ingredient transparency.
- Estimate your ingredient and energy costs per batch.
- Compare to the average retail price of a similar quality product.
- Factor in time, tools, and learning curve for homemade items.
The financial advantage of making things yourself becomes clearer with scale – the more you make, the more you save.
Tools and Equipment: One-Time Investments or Ongoing Expenses?
When setting up a DIY workspace, one of the first questions to address is whether the gear you acquire will serve you long-term or require periodic replacement. The answer largely depends on the quality, maintenance, and nature of the tools you choose. Power tools like drills or saws, when purchased from reputable brands, typically last several years with proper care. However, consumables such as blades, sanding discs, and glue sticks are recurring costs that can add up quickly.
Beyond the tools themselves, it's important to consider auxiliary equipment–items like clamps, measuring instruments, and safety gear. These are usually one-time purchases, but accidental damage or wear-and-tear may turn them into repeat buys. Understanding which items fall into which category can help you build a realistic budget for your homemade projects.
Breakdown of Costs
Item | Initial Purchase | Needs Replacement |
---|---|---|
Electric Drill | ✔ | ✘ |
Saw Blades | ✔ | ✔ (frequent) |
Protective Goggles | ✔ | ✔ (occasional) |
Wood Glue | ✔ | ✔ (constant) |
Even high-quality tools degrade faster without regular maintenance–clean, oil, and store them properly to extend lifespan.
- Long-Term Gear: Workbench, clamps, levelers, safety gear
- Short-Term Consumables: Fasteners, adhesives, sandpaper
- Invest in quality tools upfront.
- Track consumable usage to avoid overspending.
- Schedule maintenance to maximize longevity.
How to Track Hidden Costs in Homemade Production
Homemade production often appears cost-effective, but concealed expenses can distort the actual investment. It's critical to identify overlooked financial and time-related inputs to assess true efficiency. These indirect costs often accumulate unnoticed, affecting profitability and sustainability.
To uncover these hidden burdens, a structured evaluation is required. This involves monitoring material wastage, accounting for tool depreciation, and evaluating the cost of personal time. Proper tracking methods can reveal insights that improve decision-making and optimize resource allocation.
Practical Methods for Identifying Indirect Expenses
Tip: Always calculate your time value per hour and include it in overall project cost estimates.
- Record supply loss: Keep a log of unused or spoiled raw materials.
- Monitor utility consumption: Note increases in electricity, gas, or water during production periods.
- Track equipment usage: Estimate wear and tear on appliances and tools over time.
- Define time spent per task using a stopwatch or time-tracking app.
- Log frequency and cost of tool replacements or repairs.
- Include packaging and transport expenses in your calculations.
Category | Typical Hidden Costs |
---|---|
Labor | Unpaid personal time, multitasking inefficiency |
Utilities | Increased energy bills due to prolonged usage |
Materials | Scrap, spoilage, overbuying |
Tools | Maintenance, depreciation, replacement |
Volume and Batch Size: How Scale Impacts Cost
Producing items at home in small amounts can lead to higher per-unit expenses due to limited bulk purchasing and increased time investment. Ingredients, packaging, and energy costs scale inefficiently when working with minimal quantities, making each unit more expensive to create.
In contrast, increasing production volume often results in better cost-efficiency. Larger batches allow for the use of wholesale supplies, reduce waste, and optimize time spent per unit. However, this scale-up may require additional equipment or storage, which introduces new fixed costs.
Key Considerations When Scaling Up
- Ingredient Procurement: Buying in bulk lowers the cost per unit but requires upfront investment.
- Labor Efficiency: Time spent per unit drops significantly with larger batches.
- Utilities: Energy costs per unit decrease when using full oven loads or longer machine cycles.
- Storage: Larger batches may need cold storage, shelf space, or containers.
Scaling up improves cost-efficiency but adds complexity–balance is key to avoid overproduction and waste.
- Calculate per-unit cost for small vs. large batches.
- Identify fixed vs. variable costs.
- Assess storage, packaging, and shelf life constraints.
Batch Size | Cost per Unit | Time per Unit |
---|---|---|
10 units | $3.20 | 15 min |
50 units | $2.10 | 8 min |
200 units | $1.35 | 4 min |
Packaging and Presentation: Hidden Costs in DIY Projects
When working on a DIY project, it’s easy to overlook the costs associated with packaging and presentation. While the materials for the main creation often take center stage in the budget, the cost of wrapping, labeling, and presenting the final product can be substantial. These expenses can sneak up on you, especially if you're aiming for a professional finish. In fact, proper packaging not only ensures the product’s safety but also plays a key role in its appeal to customers or recipients.
It's important to understand that presentation involves more than just a simple box or wrap. The choice of packaging materials, design, and customization can add up quickly, and you may find yourself spending more than expected. Below are a few aspects that often go unnoticed in DIY projects:
- Packaging Materials – Boxes, tapes, labels, and padding materials all contribute to the overall cost.
- Customization – Personalized packaging for a professional look can require additional resources like custom prints or premium wrapping.
- Shipping Costs – If you're planning to send your product, shipping and handling fees must be considered in the overall cost.
Important considerations:
When deciding on packaging, balance aesthetics with functionality. The right packaging can elevate the perceived value of your product, but don't overspend on unnecessary features.
Cost Breakdown
Packaging Item | Estimated Cost |
---|---|
Basic Box | $1.50 - $3.00 |
Custom Labels | $0.50 - $2.00 per label |
Bubble Wrap | $0.25 - $0.50 per unit |
Shipping | $5.00 - $20.00 depending on weight and location |
Always factor in shipping and handling costs early in the planning stage to avoid last-minute surprises.
How to Estimate and Reduce Waste in Homemade Processes
Estimating and minimizing waste is crucial in homemade processes, as it not only helps in managing resources but also ensures a more sustainable and cost-effective approach. By analyzing the materials used and the efficiency of each step, you can identify areas where waste occurs and take corrective measures. The first step in this process is to measure and track the materials consumed during each task.
One effective method to estimate waste is through the use of specific tracking tools. This can involve calculating the ratio of raw materials to final product output. By doing so, you can determine how much excess material is left over or discarded at each stage. The goal is to identify inefficiencies and reduce them.
Methods to Estimate Waste
- Material tracking: Record the exact amounts of materials used and compare it to the finished product weight/volume.
- Step analysis: Break down each step of the process to find stages where material loss is high.
- Performance benchmarks: Set optimal material usage targets and measure your output against them.
Ways to Reduce Waste
- Refining processes: Streamline steps to minimize material loss during each phase of production.
- Optimizing material use: Experiment with different material types or processing methods to use less without sacrificing quality.
- Recycling and reusing: Where possible, recycle leftover materials for future use.
Key Takeaway: Consistently tracking and analyzing each step in the process can provide valuable insights into how to reduce waste and improve efficiency.
Waste Comparison Table
Material | Initial Amount (kg) | Final Product (kg) | Waste (kg) | Waste Percentage |
---|---|---|---|---|
Flour | 10 | 8 | 2 | 20% |
Sugar | 5 | 4.5 | 0.5 | 10% |
Eggs | 3 | 2.8 | 0.2 | 6.67% |