Vocational Technical Skills
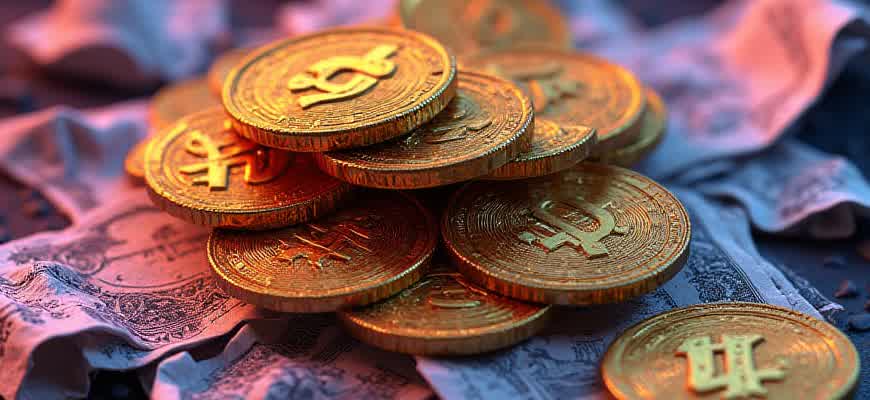
Modern industries demand a workforce equipped with specific, job-oriented competencies. These include mechanical troubleshooting, electrical wiring, automotive diagnostics, and computer-aided design. Such skills are typically acquired through focused instruction and real-world application.
- Engine maintenance and repair
- Blueprint interpretation
- Installation of industrial machinery
- Network configuration and system security
Note: Employers prioritize candidates who can demonstrate proficiency through certifications and hands-on experience.
To ensure comprehensive development, training programs often follow a structured pathway:
- Introduction to foundational principles
- Guided practice in controlled environments
- Supervised on-the-job training
- Independent project execution
Skill Area | Typical Duration | Certification |
---|---|---|
HVAC System Installation | 6 months | EPA Section 608 |
Precision Welding | 4 months | AWS Certified Welder |
IT Support and Networking | 5 months | CompTIA A+ |
How to Select a Technical Training Program Aligned with Labor Market Needs
Before committing to any specialized training, it's essential to examine which technical occupations are currently experiencing a hiring surge. Programs that lead to positions in healthcare technology, renewable energy maintenance, or advanced manufacturing offer higher chances of employment and career stability. Focus on gaining qualifications that align with sectors where automation or globalization has less impact.
Researching regional labor statistics and industry growth projections can help you determine which certifications or associate degrees are most likely to translate into job offers. Look for credentials that are either state-licensed or nationally recognized, ensuring they meet employer expectations.
Steps to Evaluate and Select a High-Demand Career Path
- Identify industries with growing employment rates using government labor reports.
- Compare the job placement rates of graduates from different vocational schools.
- Consult with local employers about their preferred qualifications and training sources.
According to the U.S. Bureau of Labor Statistics, sectors such as electrical technology, medical diagnostics, and CNC machining are projected to see a double-digit employment increase over the next decade.
- Healthcare Technology: High demand for radiologic technicians and medical lab assistants.
- Skilled Trades: Consistent need for electricians, welders, and HVAC specialists.
- IT Support and Networking: Fast-growing field with many entry points via certificates.
Field | Expected Growth | Average Salary (USD) |
---|---|---|
Wind Turbine Technicians | 44% | 56,000 |
Medical Equipment Repairers | 17% | 53,000 |
Industrial Machinery Mechanics | 19% | 58,000 |
Credentials Needed to Start in Technical Fields
Launching a career in hands-on industries such as automotive repair, HVAC maintenance, or IT support typically requires specific certifications that validate practical abilities. These qualifications are often obtained through short-term training programs or vocational schools and are essential for employers to assess foundational competence.
Many technical entry roles mandate nationally recognized credentials that demonstrate a candidate's readiness to handle industry-standard tools and protocols. Without these, applicants may face limited job opportunities or lower starting wages.
Common Certifications by Sector
- Information Technology: CompTIA A+, Cisco Certified Technician (CCT)
- Electrical and Electronics: OSHA 10/30, EPA 608 (for HVAC)
- Automotive: ASE Entry-Level Certification
- Welding: AWS Certified Welder Program
Note: Employers often prioritize candidates with certifications issued by accredited bodies such as CompTIA, ASE, or OSHA.
- Identify the field of interest
- Research required entry-level credentials
- Enroll in an accredited training program
- Pass the certification exam
Industry | Essential Certificate | Issuing Organization |
---|---|---|
HVAC | EPA Section 608 | U.S. Environmental Protection Agency |
IT Support | CompTIA A+ | Computing Technology Industry Association |
Automotive Repair | ASE Entry-Level | National Institute for Automotive Service Excellence |
Tools and Equipment Commonly Used in Vocational Training
Vocational programs rely on specialized instruments to simulate real work environments. These tools vary depending on the field of study but generally include both hand-operated and powered devices for precise, skill-based tasks. For instance, a course in metal fabrication would require welding machines, whereas a carpentry module would emphasize the use of saws and measuring tools.
Effective skill-building also depends on familiarizing students with industry-grade gear. This includes diagnostic devices in automotive courses, multimeters in electrical training, and programmable controllers in industrial automation. Proper handling and maintenance of such equipment are essential parts of the learning process.
Commonly Used Instruments by Field
- Automotive Technology: torque wrench, OBD-II scanner, hydraulic lift
- Construction and Carpentry: circular saw, spirit level, framing square
- Electrical Installation: wire stripper, circuit tester, conduit bender
- Welding: MIG welder, angle grinder, welding helmet
Mastery of these devices enhances not only technical expertise but also workplace safety and operational efficiency.
- Inspect tools before each use to ensure functionality.
- Use personal protective equipment when operating machines.
- Follow manufacturer instructions for calibration and upkeep.
Tool | Application | Training Field |
---|---|---|
Digital Multimeter | Measuring voltage, current, resistance | Electrical Engineering |
Bench Grinder | Sharpening tools and shaping metal | Metalworking |
Lathe Machine | Precision cutting and shaping | Machining |
Steps to Transition from Classroom Training to On-the-Job Application
Acquiring technical competencies in a controlled learning environment is only the first phase. The next critical step is integrating these competencies into real-world workflows, where time constraints, safety standards, and team collaboration all come into play.
To ensure a smooth move from theory to practice, learners need a structured pathway. This includes preparing for real tasks, understanding workplace-specific procedures, and receiving proper mentorship during the transition phase.
Structured Approach to Applying Technical Skills in the Workplace
- Review Core Procedures: Revisit the standard operating protocols and compare them to what was taught during training.
- Shadow Experienced Technicians: Observe how senior staff handle tools, follow safety procedures, and manage workflow.
- Gradual Task Involvement: Start with simple responsibilities, increasing complexity as confidence and competence grow.
Hands-on experience should begin with clear supervision. Independent task execution should only be allowed after consistent demonstration of competence.
- Daily check-ins with a mentor or supervisor
- Feedback sessions after each shift
- Documentation of completed tasks and reflections
Phase | Key Focus | Expected Outcome |
---|---|---|
Initial Observation | Understand tools and workflows | Familiarity with the environment |
Assisted Execution | Perform tasks under supervision | Skill refinement and error reduction |
Independent Work | Apply skills autonomously | Full job readiness |
How to Build a Portfolio to Showcase Your Technical Skills
Creating a well-organized portfolio is essential for anyone aiming to demonstrate hands-on abilities in areas like electrical engineering, welding, computer-aided design, or automotive repair. A portfolio provides concrete evidence of completed projects, certifications, and improvements over time, allowing employers or clients to assess your qualifications quickly and visually.
To start, gather tangible proof of your competencies–this includes annotated images of projects, performance test results, and technical reports. Document your process from start to finish to highlight problem-solving approaches and precision work.
Key Components of a Technical Portfolio
- Project Descriptions: Include objectives, tools used, and outcomes.
- Visual Evidence: Add photos, blueprints, or screenshots where applicable.
- Certifications: Attach scanned copies of any official documents or trade licenses.
- Reflections: Write brief notes on lessons learned or how you overcame challenges.
Always include only your original work. If a project was completed in a group, clearly state your personal contribution.
- Compile all relevant files and visuals in a single folder.
- Create a digital version (PDF or website) for easy sharing.
- Review and update the portfolio quarterly to reflect new skills or completed tasks.
Item | Description | Format |
---|---|---|
Blueprint Samples | CAD drafts from recent mechanical designs | PDF or image |
Welding Projects | Before-and-after photos with technique details | Image with captions |
Electrical Work | Circuit diagrams with test results | Scanned documents |
Frequent Errors Newcomers Make in Practical Technical Work
In the early stages of learning manual trades or applied technical skills, beginners often overlook critical procedures. These missteps can hinder their progress, damage equipment, or compromise safety. Understanding the most frequent oversights is crucial for developing reliable habits and maintaining professional standards.
One common problem is rushing through tasks without properly understanding equipment or process sequences. This haste often leads to errors that require costly rework or even pose danger in high-risk environments like electrical systems or welding setups.
Typical Missteps in Technical Practice
- Skipping safety protocols: Neglecting to wear protective gear or ignoring machine lockout procedures.
- Improper tool usage: Using the wrong tool size or type, leading to equipment damage or personal injury.
- Neglecting measurements: Failing to double-check dimensions or tolerances before cutting or assembling parts.
- Not reading technical documentation: Manuals, diagrams, or wiring schematics are often overlooked, leading to incorrect assembly or wiring.
- Overconfidence in theory: Applying textbook concepts without adapting them to real-world variability or tolerances.
Always verify calibration of your instruments before critical measurements – inaccurate tools result in inaccurate outcomes.
Issue | Consequence |
---|---|
Bypassing grounding checks | Risk of electrical shock or fire |
Loose mechanical joints | System failure under load |
Inadequate soldering technique | Intermittent electrical connections |
How Employers Assess Candidates with Vocational Training
When employers evaluate job applicants with a vocational training background, they focus on specific competencies that are directly applicable to the job. Unlike traditional academic education, vocational training prepares individuals with practical skills tailored to particular industries. Employers are keen to ensure that candidates have the necessary hands-on experience and technical knowledge to perform their tasks efficiently. This approach helps employers minimize the training time required once the candidate is hired.
In addition to technical skills, employers also look for candidates who exhibit strong work ethics, reliability, and the ability to adapt to new technologies and methodologies. Evaluating these factors allows employers to assess how well a candidate will fit into the workplace and contribute to the overall success of the company. Below are some of the main criteria employers use when evaluating candidates with vocational training backgrounds.
Key Evaluation Factors
- Technical Proficiency: Employers check the level of skill acquired through vocational training, focusing on job-specific abilities like machinery operation, software knowledge, or electrical work.
- Work Experience: Practical work experience gained during training or internships plays a vital role in demonstrating the candidate’s ability to perform under real-world conditions.
- Problem-Solving Ability: Employers seek candidates who can quickly identify issues and apply their training to resolve problems efficiently.
Methods of Assessment
- Interviews: Employers often conduct technical interviews where candidates are asked to solve problems related to their field.
- Practical Tests: These may include on-the-job simulations to assess how candidates apply their vocational skills in real-world scenarios.
- References and Portfolios: Providing proof of completed projects or feedback from previous employers or trainers can be an important factor in the evaluation process.
Important: Employers value candidates who can demonstrate a clear understanding of their vocational skills, as well as an ability to continuously learn and adapt to evolving industry standards.
Key Competencies Employers Look for
Competency | Importance |
---|---|
Technical Skills | Essential for performing the core tasks of the job with minimal supervision. |
Workplace Readiness | Ability to integrate into the company culture and work collaboratively with teams. |
Adaptability | Capacity to learn new tools and techniques as technology evolves in the industry. |
Staying Ahead in a Rapidly Evolving Field: How to Keep Your Skills Sharp
In industries where technology is evolving quickly, it is crucial to stay updated with the latest advancements. Professionals need to actively engage in learning to remain competitive. This involves a variety of strategies, from formal education to hands-on practice. Updating your skills is not just about keeping pace with current trends but also ensuring your expertise remains relevant for future challenges.
Here are some key methods to stay at the forefront of your technical field and maintain a high level of proficiency:
Methods to Stay Updated
- Online Courses and Certifications: Enroll in online programs from recognized platforms like Coursera, Udemy, or LinkedIn Learning. These platforms offer industry-specific certifications that demonstrate updated knowledge.
- Networking and Professional Communities: Join online forums, attend webinars, or participate in industry-specific groups. Engaging with peers and experts allows you to exchange ideas and stay informed on best practices.
- Workshops and Conferences: Participate in hands-on workshops or attend industry conferences to learn directly from innovators and leaders in your field.
Approaches for Continuous Learning
- Practice Regularly: Set aside time each week to apply what you have learned in real-world scenarios. This could involve personal projects, open-source contributions, or collaborations with colleagues.
- Use New Tools and Software: Make it a habit to experiment with new technologies and tools that emerge in your field. Staying adaptable ensures that you are prepared for changes in the workplace.
- Mentorship: Seek out mentors who can offer guidance based on their experience and perspective. A mentor can provide valuable feedback and help you navigate complex areas in your profession.
"Learning is a lifelong journey. Those who remain committed to growing their skills will always be in demand." - Industry Expert
Key Resources to Consider
Resource | Benefit |
---|---|
MOOCs (Massive Open Online Courses) | Flexible learning, affordable, industry-recognized certifications |
Professional Certifications | Specialized knowledge, credibility in the job market |
Tech Meetups | Networking, sharing practical knowledge, community support |