Skills Needed to Be a Technician
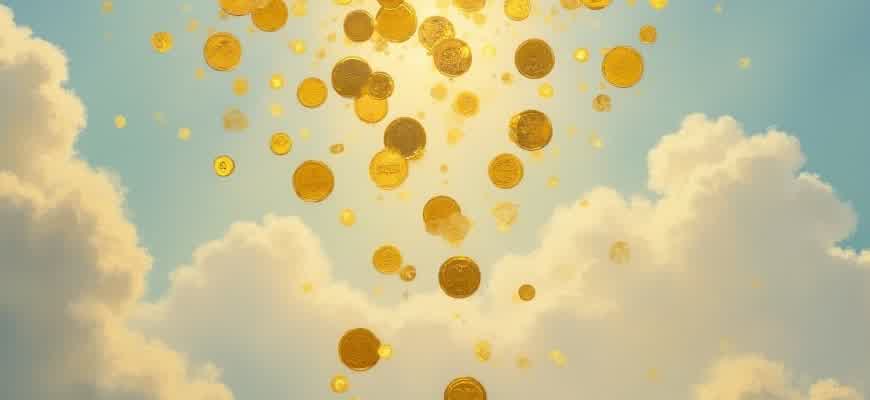
Technicians must possess a diverse set of skills to effectively perform their duties. The technical expertise is just the beginning; practical problem-solving, communication, and attention to detail are also crucial for success in this field.
Key Skills Required:
- Technical Proficiency: Deep knowledge of the systems, tools, and processes relevant to the technician's specialization.
- Problem-Solving Ability: Capability to diagnose and repair issues swiftly and accurately, often under time pressure.
- Attention to Detail: Precision in every task, from routine maintenance to complex repairs.
- Communication Skills: Ability to clearly explain issues and solutions to both technical and non-technical personnel.
Essential Technical Knowledge Areas:
- Electrical systems
- Mechanical systems
- IT infrastructure and troubleshooting
- Safety protocols and standards
"A technician's expertise isn't limited to technical knowledge; their ability to communicate effectively and solve problems efficiently is just as important."
Below is a table illustrating the core technical competencies for various types of technicians:
Technical Field | Core Competencies |
---|---|
Electrical Technician | Understanding circuits, wiring, and troubleshooting electrical faults. |
Mechanical Technician | Proficiency in mechanical systems, including engines, pumps, and HVAC systems. |
IT Technician | Experience in networking, hardware repair, and software troubleshooting. |
Mastering Basic Troubleshooting Techniques
In the field of technical work, the ability to effectively troubleshoot issues is crucial for success. Mastering basic troubleshooting methods not only saves time but also ensures that problems are resolved efficiently. Whether dealing with hardware malfunctions or software glitches, understanding the root cause is key to restoring functionality quickly and accurately.
Technicians need to approach problems in a structured way. Breaking down issues step-by-step helps to avoid confusion and ensures no detail is overlooked. A systematic approach also allows technicians to eliminate potential causes one at a time, narrowing down the solution faster.
Common Troubleshooting Steps
- Identify the Problem: Begin by understanding the symptoms of the issue and gathering information about when and how it occurs.
- Research Possible Causes: Based on the symptoms, explore common causes related to the problem.
- Test Potential Solutions: Implement fixes or changes one at a time and observe the results.
- Evaluate Results: If the issue persists, review previous steps and adjust your approach accordingly.
Remember: Patience and methodical thinking are essential. Jumping to conclusions can lead to overlooking the real issue, resulting in wasted time and effort.
Steps to Improve Troubleshooting Skills
- Practice regularly: Familiarity with common issues enhances your ability to diagnose them quickly.
- Stay organized: Maintain notes and logs of past issues to recognize recurring problems.
- Learn from others: Collaborating with colleagues can provide new perspectives on solving technical problems.
Tools and Techniques
Tool | Purpose |
---|---|
Multimeter | Used to measure electrical values such as voltage and resistance. |
Diagnostic Software | Helps identify software-related issues and perform system checks. |
Cable Tester | Verifies the integrity of cables, ensuring proper data transmission. |
Understanding System Components and Their Functions
In the role of a technician, a clear understanding of the different components within a system and their respective functions is crucial. Whether dealing with computer hardware, industrial machines, or network systems, each component serves a specific purpose that contributes to the overall performance. Knowing how these parts interact ensures more effective troubleshooting, maintenance, and optimization.
Components can vary greatly depending on the system, but they can generally be categorized into hardware, software, and supporting systems. Each part relies on others to work properly, and understanding their relationships and functions is key to diagnosing issues and improving system efficiency.
Key Components of a System
- Processor (CPU): Responsible for executing instructions and performing calculations that drive the system.
- Memory (RAM): Temporarily stores data that is being actively used by the processor.
- Storage: Holds long-term data, such as files, programs, and system configurations.
- Input/Output Devices: Allow interaction between the system and users, such as keyboards, monitors, and printers.
- Power Supply: Provides the necessary energy for the system's operation.
- Network Interface: Manages data exchange between the system and external networks or devices.
Functionality Breakdown
Understanding how these components function together can be illustrated as follows:
Component | Function |
---|---|
Processor (CPU) | Performs calculations and executes instructions for all system operations. |
Memory (RAM) | Provides temporary storage for data being processed by the CPU, ensuring fast access. |
Storage | Stores system software, applications, and user data for long-term access. |
Input/Output Devices | Enable user interaction and data exchange between the system and the external world. |
Power Supply | Delivers the necessary electrical energy to all components of the system. |
Network Interface | Handles communication with other devices or networks, allowing data transmission and remote access. |
Understanding the role of each system component not only aids in efficient troubleshooting but also helps in optimizing system performance and ensuring longevity.
How to Carry Out Regular Maintenance and Inspections
Regular maintenance and inspections are essential for ensuring that equipment and systems operate smoothly over time. As a technician, developing a structured approach to these tasks can minimize downtime, extend the lifespan of machinery, and prevent costly repairs. Technicians should be familiar with the manufacturer’s guidelines and maintain a routine schedule based on the specific needs of the equipment they service.
Maintenance procedures typically consist of several key activities: cleaning, checking for wear and tear, lubricating moving parts, and testing components for functionality. Inspections are crucial for identifying any potential issues before they become significant problems. A thorough understanding of how each system operates and what to look for during inspections is vital to success.
Steps to Perform Regular Maintenance and Inspections
- Follow the manufacturer’s recommended maintenance schedule.
- Perform visual inspections of all components, checking for signs of damage or wear.
- Lubricate moving parts as specified to ensure smooth operation.
- Test key functions of equipment to verify everything is operating properly.
- Record maintenance activities to keep track of repairs and replacements.
Routine Maintenance Checklist
Activity | Frequency | Notes |
---|---|---|
Visual Inspection | Weekly | Look for any signs of wear, leaks, or damage. |
Lubrication | Monthly | Ensure all moving parts are properly lubricated to prevent friction. |
Component Testing | Quarterly | Test for functionality and check electrical connections for reliability. |
Tip: Always use the correct tools and parts for maintenance to avoid causing damage. Refer to the equipment’s manual for specific instructions.
Importance of Consistent Inspections
- Prevents minor issues from turning into major breakdowns.
- Helps maintain safety standards, ensuring equipment is operating without posing a hazard.
- Improves overall system performance and efficiency.
- Enhances the lifespan of machinery by addressing issues early on.
Critical Thinking for Solving Complex Problems in Real Time
When a technician faces an issue in a high-pressure environment, quick and effective decision-making is essential. This requires the ability to evaluate problems from different angles, weigh available options, and select the most efficient solution. Critical thinking is not just about identifying the problem; it's about recognizing patterns and understanding the deeper cause behind the failure. The technician's response must be well-structured, ensuring minimal downtime while restoring functionality.
In real-time scenarios, technicians must navigate through multiple variables, often without the luxury of extended troubleshooting time. This dynamic environment demands the ability to analyze data rapidly, prioritize tasks, and implement fixes under time constraints. Mastery of critical thinking skills ensures that technicians can manage complex issues while maintaining operational stability.
Steps for Effective Problem-Solving
- Identify and Define the Issue: Gather all relevant information to understand the problem's scope.
- Evaluate Possible Causes: Quickly eliminate unlikely scenarios and focus on plausible causes based on available data.
- Formulate Potential Solutions: Consider all possible solutions, taking into account time, resources, and impact.
- Implement the Solution: Execute the best solution while monitoring for unintended side effects.
- Review the Outcome: Assess the effectiveness of the solution and adjust if necessary.
Key Areas of Critical Thinking for Technicians
- Analytical Skills: Being able to break down a problem into smaller, manageable components.
- Decision-Making Speed: Making quick decisions while avoiding hasty mistakes that could worsen the situation.
- Prioritization: Focusing on the most impactful issues first and addressing less critical problems later.
- Adaptability: Adjusting solutions in real-time as new information becomes available.
"A technician’s ability to think critically and solve problems on the fly is directly correlated to the success of the operation. Quick fixes that lack depth can cause long-term issues, whereas well-considered solutions maintain both efficiency and sustainability."
Example of Real-Time Problem-Solving
Scenario | Immediate Action | Long-Term Solution |
---|---|---|
System failure in a production line | Quickly assess the malfunctioning component and isolate the problem. | Investigation to find root cause and implement permanent fixes to prevent recurrence. |
Network outage in an office | Identify whether it's an internal or external issue, then apply temporary fix. | Review network infrastructure and upgrade faulty hardware or software components. |
Adapting to Technological Advancements and Tools
Technicians must continuously update their knowledge and skillset to keep up with the rapid pace of technological progress. As industries evolve, the tools and technologies used in daily operations change, demanding a flexible and proactive approach from those in technical fields. Staying relevant involves not only learning new software and hardware but also mastering how to troubleshoot and maintain modern equipment that might not have existed just a few years ago.
Adapting to these advancements requires both theoretical understanding and practical application. Technicians should be proficient in utilizing cutting-edge tools, staying informed about software updates, and understanding new hardware components. This adaptability is essential for maintaining efficiency and ensuring high-quality service in ever-evolving environments.
Key Strategies for Adaptation
- Continuous Learning: Enroll in relevant courses, attend workshops, and stay updated with industry trends.
- Hands-on Experience: Practice using new tools and technologies regularly to build familiarity.
- Collaboration: Work with experts and colleagues to share knowledge and solve complex issues.
Benefits of Keeping Up with Technological Advancements
Benefit | Explanation |
---|---|
Improved Efficiency | Familiarity with new tools allows technicians to perform tasks faster and with greater precision. |
Enhanced Problem-Solving | Knowledge of advanced technology helps technicians diagnose and fix issues more effectively. |
Job Security | Technicians who adapt to new technologies are in high demand and less likely to be replaced by automation. |
Important: Technicians who fail to stay updated with advancements risk becoming obsolete in a highly competitive field.
Improving Communication Skills for Client Interactions
Effective communication is essential for technicians working with clients. It helps in building trust and delivering clear information regarding technical issues. A technician must be able to convey complex concepts in a way that the client can easily understand, ensuring that both parties are aligned in expectations and solutions. The ability to actively listen and address client concerns is also crucial for successful interactions.
To improve communication skills, technicians should focus on both verbal and non-verbal techniques. Adapting language to suit the client's level of understanding, maintaining a professional tone, and using body language effectively are all aspects that contribute to a positive interaction. Moreover, refining problem-solving communication can make a big difference in client satisfaction.
Key Skills for Effective Communication
- Active Listening: Pay close attention to what the client is saying, ensuring their concerns are fully understood.
- Clear Explanation: Break down technical terms and jargon into simple language that the client can easily grasp.
- Empathy: Understand and acknowledge the client's frustration or confusion, which helps in building rapport.
Steps to Enhance Communication Skills
- Practice Listening: Focus on understanding the message, not just the words. Give the client time to explain their issue in detail.
- Ask Clarifying Questions: When in doubt, ask questions to ensure accurate understanding of the problem.
- Summarize the Issue: Restate the client’s concerns in your own words to confirm mutual understanding.
"The most important thing in communication is hearing what isn't said." – Peter Drucker
Handling Difficult Situations
Scenario | Approach |
---|---|
Client upset about a delayed service | Remain calm, acknowledge their frustration, and provide a clear update on the situation. |
Confusion over technical jargon | Use simple analogies or visual aids to explain the issue in an understandable manner. |
Time Management for Handling Multiple Projects Simultaneously
In the role of a technician, the ability to manage time effectively is crucial when handling multiple projects at once. Technicians often face deadlines and competing priorities, requiring them to make the best use of their time. Proper planning and organization allow technicians to avoid stress and meet expectations without compromising quality. Time management is not just about allocating hours; it involves making strategic decisions to ensure each project progresses smoothly.
To stay on top of multiple tasks, technicians need a methodical approach. Breaking down large tasks into smaller steps and prioritizing them helps to create a clear path forward. Effective scheduling tools and techniques are essential for staying organized and preventing time wasted on less important activities.
Key Strategies for Time Management
- Prioritize Tasks: Focus on high-impact tasks first. Evaluate the urgency and importance of each project to ensure key objectives are met on time.
- Use Tools and Technology: Leverage project management software to track deadlines, set reminders, and collaborate efficiently with teams.
- Set Realistic Deadlines: Ensure that the deadlines set for each project are achievable within the available time frame.
- Avoid Multitasking: While it may seem efficient, working on too many tasks simultaneously can reduce productivity and quality. Focus on one task at a time.
Actionable Steps for Effective Time Allocation
- Create a Daily Schedule: Break down tasks into smaller chunks with specific deadlines for each day. This creates a sense of urgency and helps stay on track.
- Review Progress Regularly: Check the status of each project daily. Adjust priorities if necessary to ensure that time is being allocated appropriately.
- Delegate Tasks: Identify areas where others can help. Delegating non-essential tasks allows technicians to focus on more critical aspects of their work.
Important: It’s essential to review your schedule at the end of each day to assess whether the time management strategy is working or needs adjustment.
Time Allocation for Multiple Projects
Project | Priority | Time Allocation |
---|---|---|
System Upgrade | High | 10 hours/week |
Software Maintenance | Medium | 6 hours/week |
Client Support | Low | 4 hours/week |
Staying Updated with Industry Standards and Safety Guidelines
Technicians must continuously adapt to the ever-evolving technological landscape. This includes staying informed about new tools, technologies, and best practices in the field. Industry standards often change, and it is crucial for technicians to regularly update their skills and knowledge to ensure they are performing their work correctly and safely. This ensures compliance with current regulations and maintains a high level of professionalism.
Adhering to safety protocols is equally important. Technicians are often exposed to hazardous materials, machinery, and environments that require them to follow strict safety guidelines. Staying current with these protocols can prevent accidents, reduce risks, and enhance overall workplace safety. It is also essential to participate in ongoing training to recognize new safety hazards and mitigate them effectively.
Key Areas for Staying Current:
- Industry-specific certifications and training programs.
- Regularly reviewing safety manuals and updates from regulatory bodies.
- Attending workshops, webinars, and conferences.
Steps for Technicians to Follow:
- Subscribe to professional journals and magazines.
- Complete refresher courses to renew certifications and learn about new technologies.
- Engage with industry forums and online communities to share knowledge and experiences.
Important: Technicians should always prioritize safety by following the latest safety protocols provided by regulatory authorities such as OSHA or ANSI.
Example of Certification Renewal Schedule:
Certification | Renewal Frequency | Source |
---|---|---|
Electrical Safety Standards | Every 3 years | National Safety Council (NSC) |
Hazardous Materials Handling | Every 2 years | Occupational Safety and Health Administration (OSHA) |
First Aid and CPR | Every 2 years | American Red Cross |